TURN-KEY PCB ASSEMBLY: BITTELE ELECTRONICS
PCB MANUFACTURING AND ASSEMBLY
Full Turn-Key PCB Manufacturer
You can quickly get quotes and order PCB fabrication and assembly using our online system. Take advantage of exclusive automatic discounts with our tool. Our BOM pricing tool ensures you receive the lowest price for your order.
START A TURN-KEY PCB ORDER
Why IPC-A-610 Requires a Solder Joint Wetting Angle Less Than 90°
Definition and Physical Significance of Wetting Angle
The wetting angle refers to the contact angle formed between liquified solder and the substrate (such as a pad or component lead) during the soldering process. It reflects the solder’s ability to wet the substrate. According to the IPC-A-610 standard, a wetting angle less than 90° is considered acceptable, while an angle exceeding 90° may indicate a defect such as cold solder joints, incomplete wetting, or open joints.
From a materials science perspective, the wetting angle is determined by the balance of surface tensions between the solder and the substrate. A wetting angle below 90° indicates that the solder spreads well, forming a concave fillet, which signifies good metallurgical bonding with a robust intermetallic compound (IMC) and ensures both electrical connectivity and mechanical strength. Conversely, a larger wetting angle suggests poor wetting and increase potential joint failure.
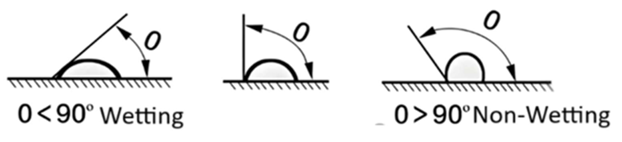
Technical Rationale for Wetting Angle Less Than 90°
A. Ensures Electrical Reliability
A wetting angle under 90° confirms that the solder forms a continuous metallurgical bond between the pad and the component lead, minimizing contact resistance and preventing issues like open circuits or high-resistance connections especially critical in high frequency or high-power applications. IPC-A-610D explicitly states that poor wetting (e.g., wetting angle > 90°) can lead to electrical instability due to oxidation or microcracks.
B. Enhances Mechanical Strength
A concave solder fillet helps distribute mechanical stress (e.g., vibration or impact) across the joint. In contrast, ball-shaped solder joints with large wetting angles concentrate stress, increasing the risk of cracking. For example, if a cylindrical component lead shifts by more than 50% laterally or 25% vertically, poor or insufficient wetting can compromise mechanical stability.
C. Indicator of Process Control
The wetting angle serves as a composite indicator of key soldering process parameters such as temperature, time, and solder composition. By standardizing this angle, IPC helps define a controllable process window to ensure consistency. For instance, during hand soldering, if the temperatures is below 240°C may result in insufficient heat, causing cold solder joints manifested as unusually high wetting angles.
Industry Practice and Scientific Basis for the Wetting Angle Standard
A. Material Compatibility
Different solder alloys (e.g., Sn-Pb vs. lead-free) have varying wetting characteristics. Lead-free solders like Sn-Ag-Cu have higher surface tension and typically larger wetting angles. However, IPC standards uniformly require angles < 90° to ensure cross-material compatibility and reliability.
B. Quantitative Defect Criteria
IPC standards use the wetting angle as a primary metric to classify solder joints as Acceptable, Process Indicator, or Defective
- Cold Joint: Rough surface, abnormal wetting angle, often with loose crystalline or porous solder structure.
- Open Joint: Wetting angle >90°, solder only partially adheres to the pad or lead.
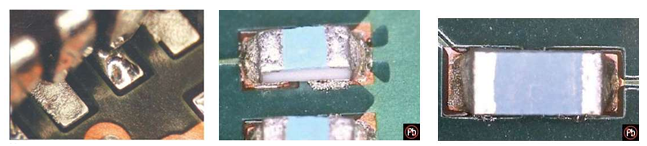
C. Long-Term Reliability in High-Reliability Applications
In aerospace and military electronics, wetting angle requirements are even stricter. For example, QJ standards specify precise soldering temperatures (e.g., 225±2°C) for sensitive components like MLCCs to ensure proper wetting and avoid thermal shock damage.
Exceptions and Special Considerations in IPC Standards
While the wetting angle is a core criterion, IPC allows certain exceptions:
A. Design-Driven Wetting Angle Deviations
If solder extends beyond the pad area due to design requirements (e.g., into the solder mask region), IPC may still consider it acceptable even if the local wetting angle exceeds 90° (see C & D).
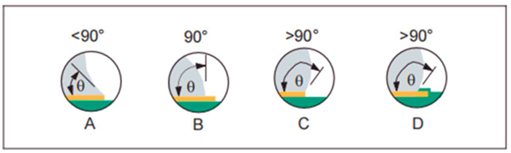
B. Lead-Free Solder Characteristics
While lead-free joints may appear dull or rougher in texture, IPC allows for slightly larger wetting angles (still < 90°), as long as solder coverage and bonding quality are within specification.
Conclusion
The IPC-A-610 standards for a wetting angle less than 90° is based on comprehensive foundation of materials science, process control, and reliability assurance. It provides a measurable criterion for solder joint quality and ensures robust electrical and mechanical performance across applications from consumer electronics, automotive, aerospace, and defense sectors.
As solder materials and packaging technologies evolve, IPC standards may continue to refine wetting angle-based criteria. However, the fundamental principle remains unchanged by ensuring interconnect reliability through adequate wetting behavior will continue to be a cornerstone of electronic assembly standards.
Please contact us to learn more about our production capabilities or to submit your design files for a formal quotation. You can contact us via phone at 1-416-800-7540 or by email at sales@7pcb.com.
Related Articles:
Please briefly describe the information you are seeking in the search bar below.