TURN-KEY PCB ASSEMBLY: BITTELE ELECTRONICS
PCB MANUFACTURING AND ASSEMBLY
Full Turn-Key PCB Manufacturer
You can quickly get quotes and order PCB fabrication and assembly using our online system. Take advantage of exclusive automatic discounts with our tool. Our BOM pricing tool ensures you receive the lowest price for your order.
START A TURN-KEY PCB ORDER
Which Soldering Defects are Related to the Incorrect Setup?
As shown in the figure below, there are four different zones in a typical refow profile – pre-heat, pre-heat and soak, reflow, and cooling zone. The incorrect setup with zone temperatures and times will cause different soldering defects.
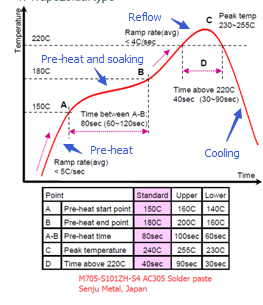
-
Pre-heat zone (from room temperature to 150°C)
-
Solder paste collapse -- ramp up too fast
The solvent in flux cannot vapour thoroughly, so the viscosity of the solder paste will be decreased and cause the paste collapse -
Soldering ball -- ramp up too fast
The solvent in flux vapours out too fast, causing some tiny paste areas to separate from the major paste area and forming individual solder balls around the component. -
Solder splash – ramp up too fast
Same as soldering ball. -
Poor wetting – ramp up too slow
Solder paste is oxidizing if the pre-heat too long.
-
Solder paste collapse -- ramp up too fast
-
Pre-heat and soak zone (from 150°C to 180°C)
-
Tombstone -- ramp up too fast
The PCB and components didn’t get an even heat up. -
Void -- ramp up too fast
The solvent in flux escaped too quickly. -
Poor solder joint fillet -- ramp up too slow
The flux lost its activity once it stayed soaking too long.
-
Tombstone -- ramp up too fast
-
Reflow zone (above 217°C ~220°C for SAC305 solder paste)
-
Component damaged – peak temperature is too high
Once the peak temperature is over 260°C and stays there for more than 10 sec, most of components will be damaged. -
Cool solder -- peak temperature is too low or time too short
The peak temperature should be 20~25°C higher than the solder liquid point and remains there for 30~90 seconds.
-
Component damaged – peak temperature is too high
-
Cooling zone (below 217~220°C after reflow)
-
Components crack -- cooling down too fast
Components experienced thermal shock outside of their specifications. -
Increase component’s fatigue risk –cooling down too slow
The slow cooling can easily lead to an excess amount of intermetallic compounds and produce larger crystal particles together in soldering joint, reducing the fatigue strength.
-
Components crack -- cooling down too fast
Related Articles:
- How to Prevent Non-Wetting Defect during the SMT Reflow Process
- How to Prevent Solder Ball and Bridging Defects during the SMT Reflow Process
- How to Prevent the Tombstone and Open Defects during the SMT Reflow Process
- How to Prevent Solder Joint Voiding and Cold Solder Defects during the SMT Reflow Process
- An Analysis of SMT Solder Paste Printing Defects
Please briefly describe the information you are seeking in the search bar below.