TURN-KEY PCB ASSEMBLY: BITTELE ELECTRONICS
PCB MANUFACTURING AND ASSEMBLY
Full Turn-Key PCB Manufacturer
You can quickly get quotes and order PCB fabrication and assembly using our online system. Take advantage of exclusive automatic discounts with our tool. Our BOM pricing tool ensures you receive the lowest price for your order.
START A TURN-KEY PCB ORDER
What does SMT stand for?
SMT stands for surface mount technology, which is an automated PCB assembly process that places, mounts, and solders electronic components to the surface of a printed circuit board. SMT reduces the cost to manufacture PCBs while increasing the rate of production. SMT is used to manufacture PCBs used in virtually every electronic product across the world. From consumer electronics, edge computing devices, and sensor boards to industrial programmable logic controllers, SMT is used to create compact PCBs in the age of compute-intensive and space constrained applications.
SMT is an improvement over traditional through-hole technology (THT) to attach components to a PCB. With THT, the leads of electronic components are inserted through holes drilled through the PCB and soldered to the bottom of the printed circuit board, making it a time-consuming and cumbersome process. Moreover, leaded electronic components are usually larger than SMT parts and require more soldering to ensure they have a good bond to a PCB. This requires more time, hence, PCB production rates are often slower than SMT’s rates. SMT components have a much smaller footprint than THT components. The size of electronic components is critical today since space-constrained applications are common, and consumer electronic devices are increasingly miniaturized.
Background of SMT
IBM was an early adopter of the surface mounting of PCB components. In the 1960s, the first version of was called Planar Mounting. Over the next two decades, Planar Mounting evolved into what SMT is today. By 1975, SMT was employed for the manufacturing of watches and calculators. But it wasn't until the 1980s when the sizes of electronic components were drastically reduced that the use of SMT in multi-featured electronic devices became common. In 1986, surface-mounted devices (SMD) made up 10 percent of the electronics manufacturing market. Only four years later, SMDs made up the majority of all PCB assemblies. There some other terms often associated with surface-mount technology (SMT). They are:
- SMD – Surface-mount devices
- SMA – Surface-mount assembly
- SMC – Surface-mount components
- SMP – Surface-mount package
- SME – Surface-mount equipment
Comparison of SMT and THT Assembly
SMT has several advantages over the THT assembly process. Most importantly, SMT is much more efficient with faster production rates. It also is more cost-effective in terms of production set up and operation. As an automated production process, SMT eliminates human errors. To underscore what had been discussed previously, SMT enables the manufacturing of miniaturized devices due to the use of small footprint electronic components. From an engineering point of view, SMT obtains at lower resistances and inductance at connection points, thus, reduces EMI and radiated emissions, resulting in improved high frequency performance of the PCB. One key benefit of electronic components with a small footprint is more parts can be mounted in a smaller square area of PCB “real estate,” increasing the effective component density.
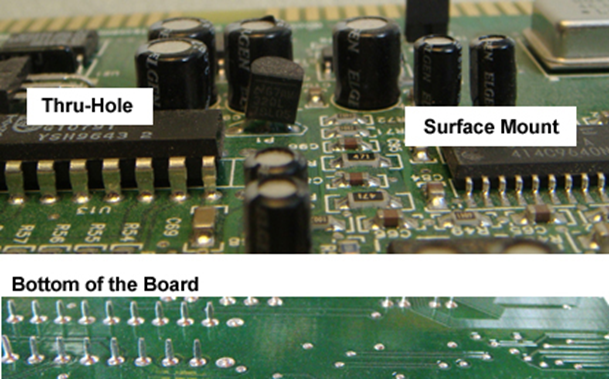
SMT possess some drawbacks as well. For repairs and rework that require desoldering components, surface mounted devices require more time and skill to remove. In addition, since SMT attaches components directly to the board, a socket cannot typically be used, as it could with THT. Since the solder connections of SMT parts are smaller than THT, they can be affected by potting compounds during thermal cycling. SMT parts are so small, their size makes it hard to repair without specialized tools and a technician with a high level of micro-electronic skills.
Description of the SMT Process
SMT is a technology, used in automated PCB assembly, where small, surface mounted devices are placed and attached to the surface of printed circuit boards. How that is done is explained in this section. To begin the assembly process, PCBs that have flat tin-lead, silver, or gold plated copper pads (solder pads) are covered with solder paste using a stencil. Once covered with solder paste, PCBs are conveyed down a production line to pick-and-place machines that take the electronic components from bins and place them in the exact location on a PCB. The PCBs are then sent through a reflow soldering oven, where the PCB and component temperature is slowly increased to prevent a condition called thermal shock. Once the PCB attains the correct temperature, it is transported to an area where it can get to a temperature high enough to melt the solder paste. The molten solder stays on the solder pads due to surface tension. After soldering has been completed, the PCB is sent to a wash because the reflow process can leave a residue or create solder balls which can cause a failure called a board short. After washing, the PCB is sent to a visual inspection station to check for any errors. Some PCB production lines use an automated optical inspection (AOI) system inside of manual visual inspections.
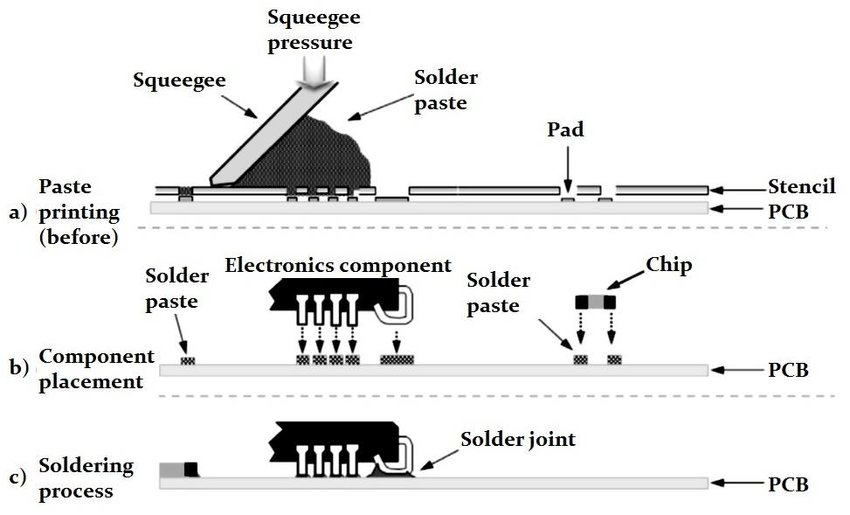
There is a difference between surface-mount technology and surface mount devices. SMDs are the actual components that are used in the circuit design, which are placed and soldered to the PCB surface. SMT is the assembly process that is used to attach the SMDs to the board. SMDs consist of a broad range of component types, include electromechanical (EM), passive, and active components. EM components are usually connectors or relays. Passive SMDs consist of resistors, capacitors, and inductors. Active SMDs are mostly some type of semiconductor, such as PMICs, microcontrollers, amplifiers, logic gates, IC sensors, diodes, and more.
Conclusion
The innovation of new technology is constantly occurring in today's world. SMT is one of those innovative technologies that has transformed how not only PCBs, but also end-user devices are manufactured, packaged, and used. SMT has been key to the development of miniaturized microchips and PCB components. SMT offers distinct advantages over through-hole technology. Faster production rates, quicker turnaround times, decreased production and labor costs, and greater efficiency are all the result of SMT. Presently, SMT is the preferred assembly process for almost all end-products with PCBs, including kitchen appliances, phones, and computing devices. While other new technologies may be developed to replace SMT in the future, for now SMT continues to dominate the market.
Related Articles:
Please briefly describe the information you are seeking in the search bar below.