TURN-KEY PCB ASSEMBLY: BITTELE ELECTRONICS
PCB MANUFACTURING AND ASSEMBLY
Full Turn-Key PCB Manufacturer
You can quickly get quotes and order PCB fabrication and assembly using our online system. Take advantage of exclusive automatic discounts with our tool. Our BOM pricing tool ensures you receive the lowest price for your order.
START A TURN-KEY PCB ORDER
What happens after your order is placed?
Bittele electronics is focused on providing all of our customers with the highest level of service possible. Once your order is placed, our team will work with you during the production progress to ensure your order goes smoothly. We have outlined the processes that take place after your order is placed, to help answer any questions you may have.
Order Release
Once your order has been placed, your account manager will release the project to the production team in China. This order release will include all of the necessary files to begin the production of your project. A tracking link will also be sent to you, along with an invoice. Our production team will then perform a DFM check to find any potential issues. For instructions on how to place an order, please follow how to place pcb fabrication assembly order.
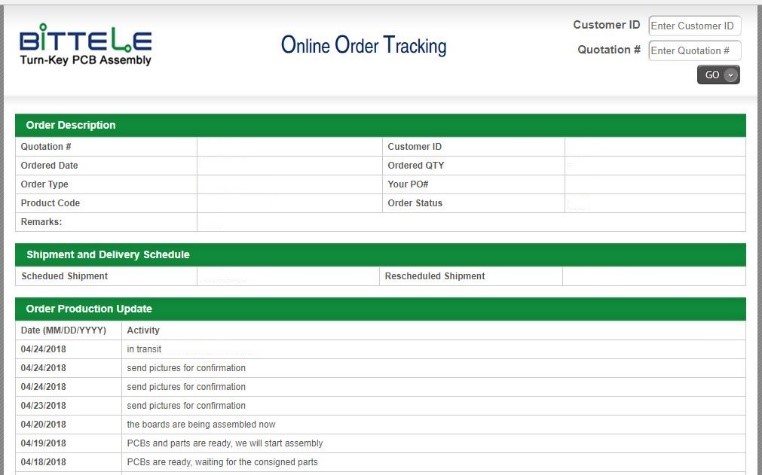
DFM Check
What is a Design for Manufacturability (DFM) check? The PCB layout topology is thoroughly reviewed to reduce the chance of any problems arising during the PCB fabrication and assembly process. The DFM check ensures that your project is within our fabrication and assembly capabilities and is the final check before production begins. Design for Fabrication (DFF) refers to when fabrication issues are addressed, while Design for Assembly (DFA) refers to when assembly issues are addressed. While DFF and DFA are the two primary components of DFM checks, there is also a third component, Design Rule Checking (DRC) that is used to complete the DFM check.
The DFM check is performed by our engineers at our production facility. All issues and questions regarding the project will be sent from the project coordinator to the client for clarification via emails.
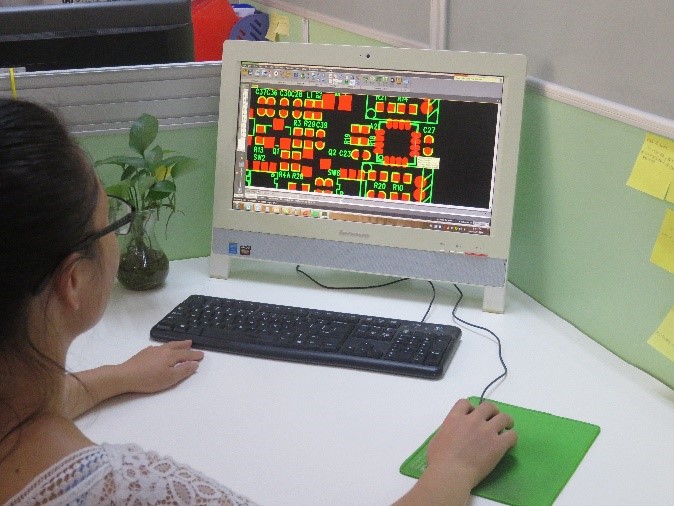
Fabrication + Parts Procurement
Once the DFM check has been completed and all outstanding issues have been resolved, the board move into fabrication. While the boards are being fabricated, our parts procurement team in Toronto has already began to purchase the parts to be used in the assembly for your project. This ensures that all the parts arrive at our production facility by the time the bare boards are complete.
Inspection/ Testing
At Bittele Electronics, electrical inspection and testing is mandatory for every project to ensure our high-quality standard is maintained. Each bare board is electrically tested for open and short circuits, while boards containing leadless parts such as a BGA will be X-Ray tested. Depending on the order size and requirements, Automated Optical Inspection (AOI) and Functional Testing may also be used.
Programing and Assembly
Upon client request, Bittele is able to provide IC programming for your production orders. Please contact either your account manager, or sales@7pcb.com with your programming requirements when you submit your RFQ, and we will review if we are able to provide a programming service for your order. For more information on this service, please see ic programming. Our standard is that SMT parts are 100% machine placed.
Shipment
Once the assembly of your order is complete, your production coordinator will send you high resolution pictures of the finished boards for your final approval. Upon your approval, we sill ship your order via FedEx international Priority, and provide you with a tracking link.
Related Articles:
Please briefly describe the information you are seeking in the search bar below.