TURN-KEY PCB ASSEMBLY: BITTELE ELECTRONICS
PCB MANUFACTURING AND ASSEMBLY
Full Turn-Key PCB Manufacturer
You can quickly get quotes and order PCB fabrication and assembly using our online system. Take advantage of exclusive automatic discounts with our tool. Our BOM pricing tool ensures you receive the lowest price for your order.
START A TURN-KEY PCB ORDER
Thermal Mass in PCBs and How Are Thermal Profiles Created
Thermal mass, also known as heat capacity, is the ability of an object to absorb and store energy as heat. The higher the thermal mass of an object the more energy is required to change its temperature.
How is this relevant to PCBAs?
At Bittele Electronics we use pick and place machines along with reflow ovens in order to assemble your boards for high accuracy, high quality, and consistency during assembly. However, in order for a board to go through our reflow ovens, a thermal profile must be created. There are many reasons a thermal profile is necessary for our reflow ovens.
One is simply for the sake of efficiency, by using a thermal profile the assembly of a board can be done with minimal time and energy wasted. Thus allowing for lower turn times and power usage throughout the assembly of a project. However, the primary reason is to make sure that the solder joints are of good quality.
Another reason is to avoid damaging the board and its components. Thermal shock, warpage, and melted components are all possibilities when bad thermal profiles are used.
The thermal mass, and thus the thermal profile of a PCB, will be optimized with the following variables:
(The following is a non-exhaustive list)
- Lead or Lead-Free Process
- Solder Paste specifications
- Material (TG140, TG170, TG180, etc)
- Dimensions (Area and Thickness)
- Density of a board
- Copper Weight
- Number of Layers
At Bittele Electronics we create the most effective thermal profiles for your boards by first classifying the boards under already existing general thermal profiles.
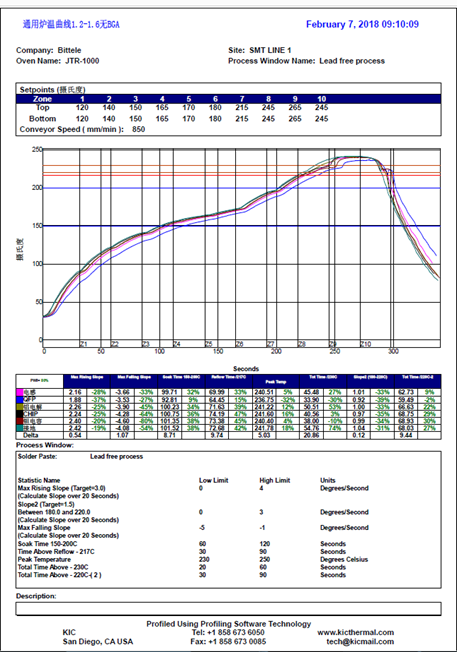
This is done by examining the properties of the PCB that affect its thermal mass, such as the ones in the list above.
If this is a new production run for a board then we use a profiler called KIC X5 Profiler to fine tune the general profile.
For a repeated production run we do not use the profile from an old run as you may think. To get the best result Bittele uses the existing profile with the KIC Profiler to verify the consistency for the reflow oven first, and then the old profile is used.
Related Articles:
- How to get real-time thermal data for a PCB?
- Reflow oven zone temperature set up and thermal profile
- Why does Bittele Use a 10 Zone Force air convection reflow oven?
- Under what conditions do you set different temperatures for the TOP and Bottom heating elements of a reflow oven?
- Circuit Designs for High Power Boards
Please briefly describe the information you are seeking in the search bar below.