TURN-KEY PCB ASSEMBLY: BITTELE ELECTRONICS
PCB MANUFACTURING AND ASSEMBLY
Full Turn-Key PCB Manufacturer
You can quickly get quotes and order PCB fabrication and assembly using our online system. Take advantage of exclusive automatic discounts with our tool. Our BOM pricing tool ensures you receive the lowest price for your order.
START A TURN-KEY PCB ORDER
When do you set different temperatures for the heating elements?
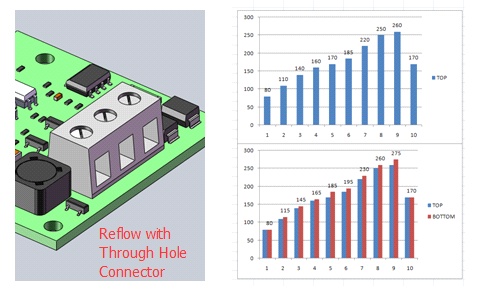
In most situations, the thermal setpoints of a reflow oven are the same for both the Top and Bottom heating elements in the same zone. But there are special cases where it is necessary to apply different temperature settings to the TOP and BOTTOM elements. The SMT process engineer should review the specific board requirements to determine the correct settings. In general, here are some guidelines for setting heating element temperatures:
- If there are through hole (TH) components on the board, and you want to reflow them with SMT components together, you may want to consider increasing the bottom element’s temperature because the TH components will block hot air circulation on the top side, preventing the the pads under TH components from receiving enough heat to make a good soldering joint.
- Most TH connector housings are made from plastic which will melt once the temperature gets too high. The process engineer must perform a test first and review the result.
- If there are big SMT components such as inductors and aluminum capacitors on board, you will also need to consider setting different temperatures for the same reason as TH connectors. The engineer needs to collect thermal data of a particular board application and adjust thermal profile several times in order to determine the correct temperatures.
- If there are components on both sides of a board, it is possible to set different temperatures as well.
Finally, the process engineer must check and optimize the thermal profile for every particular board. Quality engineers should also involved in order to inspect the solder joint. An x-ray inspection machine may be utilized for further analysis.
Related Articles:
Please briefly describe the information you are seeking in the search bar below.