TURN-KEY PCB ASSEMBLY: BITTELE ELECTRONICS
PCB MANUFACTURING AND ASSEMBLY
Full Turn-Key PCB Manufacturer
You can quickly get quotes and order PCB fabrication and assembly using our online system. Take advantage of exclusive automatic discounts with our tool. Our BOM pricing tool ensures you receive the lowest price for your order.
START A TURN-KEY PCB ORDER
A Brief Analysis of the Most Common Surface Mount Devices (SMDs)
Bittele Electronics is an experienced provider of Complete PCB Assembly for all package types, with over 10 years of industry experience in providing High-Quality PCB Assembly for Surface Mount Devices (SMDs) of all sorts. In this article, we would like to offer our clients some insight into six common types of SMDs, including the standard applications of these package types, as well as their effects on the PCB Assembly Process. In the interest of brevity, we will not delve into too much detail here with regard to the specifics of PCB design around these parts. For a complete picture of our processes where these parts are concerned, please see our individual articles on PLCC, QFP, QFN, BGA, and POP components, as well as our comprehensive DFA Guidelines document.
SOIC & SOT
The SOIC (Small Outline Integrated Circuit) and the SOT (Small Outline Transistor) are perhaps the most common type of SMDs, and are included in a majority of SMT Assembly projects today. The SOIC can be considered the surface-mount equivalent of the classic though-hole DIP (Dual-Inline Package), while the SOT is a direct SMD equivalent to the legacy through-hole SOT package.
Both of these package types are included under Bittele’s PCB Options at a Standard Price, and no additional cost or PCB Turn Time will be incurred by the presence of these types of components on your Bill of Materials (BOM). This means that our standard PCB Assembly Process is sufficient to effectively assemble SOIC and SOT components with no additional tooling or process engineering required.
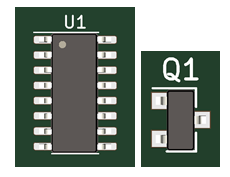
QFP
QFP (Quad Flat Package) components are most often used for microcontrollers, multi-channel codecs, and other moderately complex parts. They are generally considered the simplest option for high pin-count components, since the leads of a QFP are exposed and therefore relatively easy to inspect rework if necessary.
QFPs are also included in Bittele’s PCB Options at a Standard Price, and are treated just the same as any other SMD for the purposes of quotation and assembly. As with all SMDs, the number of pads included on the package will have some impact on the price of your quotation, but no additional cost is added for the simple existence of a QFP component in your design. These parts can be assembled using standard Reflow Soldering, and inspected using Automated Optical Inspection (AOI) in tandem with multi-stage Visual Inspection.
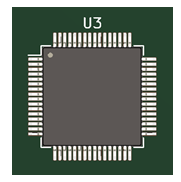
QFN
The QFN (Quad Flat No-Lead) package is similar to the QFP, with the notable difference that the electrical contacts of these devices do not protrude from the body of the component. This difference allows for QFN packages to be physically smaller than equivalent QFPs, but they do require some additional attention during PCB Assembly, and generally cannot be assembled reliably by non-professional methods such as Manual Assembly.
Unlike the package types discussed above, QFN packages do require some additional attention during PCB Assembly. The most notable difference in process for these parts is that they require X-Ray Inspection as a part of the Quality Management process. For designs with only a few small QFN packages, we can sometimes waive additional costs associated with these more demanding inspection procedures, but this must be assessed on a case-by-case basis.
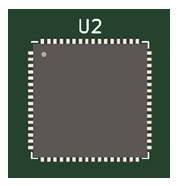
PLCC
PLCCs (Plastic Leaded Chip Carriers) are flexible options that allow for components to be mounted in a socket or soldered directly onto the PCB. These packages are particularly convenient for Prototype PCB Assembly projects, and especially those requiring IC Programming services. A socket can be used in the early iterations of the PCB, allowing ICs to be easily swapped in and out for testing purposes, and the smaller footprint of the IC itself can even be placed within the larger socket footprint so that no design change is necessary when your project moves into larger scale production.
PLCC sockets are normally treated as QFP-type components for the purposes of PCB assembly, while the PLCC components themselves are more akin to QFNs. As such, you should expect a slight difference in your PCB Assembly Quote when you switch to the more permanent solution of soldering your PLCC chip directly to the board. That being said, this cost is offset by the often considerable cost of IC sockets that will no longer need to be included on your BOM at this stage.
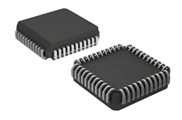
BGA
BGA (Ball Grid Array) packages are generally used for the most complex, high pin-count components on the market today, such as high-speed microprocessors and FPGAs (Field Programmable Gate Arrays). That being said, smaller BGA Variants such as the µBGA and DSBGA are sometimes used for simpler components for their smaller size compared to other package types. All BGA variants will require Reflow Soldering for their PCB Assembly, since the electrical contacts of these parts are located entirely beneath the silicon body of the IC.
Similar to QFN packages, BGAs will require additional attention from Bittele’s process engineers in the form of X-Ray Inspection. Since these parts are so complex and sensitive, and include such a multitude of pins that must all be soldered perfectly, we do require X-Ray inspection for BGA Assembly projects to ensure that we can meet our guaranteed standards of quality.
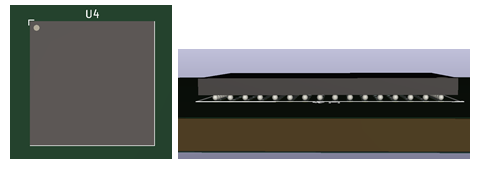
POP
POP (Part-on-Part) technology refers to a process whereby specific components can be assembled directly atop one another. Most commonly used for memory modules and their associated microprocessors, this technique allows for significant space conservation in High-Density Interconnect (HDI) designs, as well as high-speed communication between crucial devices. The bottom device is normally a large BGA component with a high pin count, and a ring of additional BGA-style contacts on the top of the device, as shown in the image below.
POP Assembly is quite complex, and requires special attention during the PCB Assembly Process. Notably, the presence of these parts on a BOM will often require multiple placement and/or Reflow Soldering cycles, which does require additional cost and lead time compared to other component types. Bittele strongly recommends that clients whose designs include POP components reach out to our PCB Customer Service team early in the design process, and send along any preliminary PCB Design Files you might have available. Early collaboration will allow our production team to prepare a strategy for your POP design ahead of time, and also to make DFM (Design for Manufacturing) or DFA (Design for Assembly) suggestions to reduce the cost and lead time associated with these complex parts.
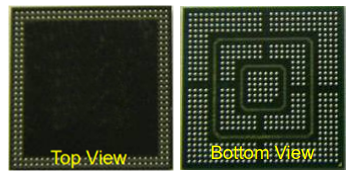
There are of course many other types of SMDs on the market, but our aim in this article is to cover the basics for our clients. The information included here can often be extrapolated to gain some idea of Bittele’s process requirements for all sorts of surface mount parts. For any questions regarding specific packages not included here, or for a more detailed look at these component types, we highly recommend the additional resources mentioned in the introductory paragraph above. You can also Contact Us any time to send along your questions, or to get an official quotation for your project today.
Related Articles:
Please briefly describe the information you are seeking in the search bar below.