TURN-KEY PCB ASSEMBLY: BITTELE ELECTRONICS
PCB MANUFACTURING AND ASSEMBLY
Full Turn-Key PCB Manufacturer
You can quickly get quotes and order PCB fabrication and assembly using our online system. Take advantage of exclusive automatic discounts with our tool. Our BOM pricing tool ensures you receive the lowest price for your order.
START A TURN-KEY PCB ORDER
Bittele’s Solder Mask Webbing Capabilities
Questions concerning solder mask webbing (also known as the solder mask bridge or solder mask dam) is often times something many clients would like to know about when considering our capabilities regarding this here at Bittele.
First of all, what is solder mask webbing? Solder mask webbing is the tiny, strip-like pieces of solder mask that remain in between the leads of any SMT part on an assembled PCB. Its purpose is to reduce the chances of solder bridging that may occur and would otherwise short circuit the component and potentially damage your board.
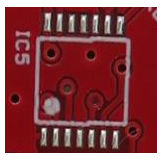
The red solder mask in between the silver pads is referred to as the solder mask webbing. When the IC5 chip is placed, the chances of solder flowing off of one pad to another pad are greatly reduced due to the presence of the solder mask webbing, thus reducing the chances of short-circuiting the component and potentially damaging the board.
As the fine pitch of components begins to get smaller and smaller, it becomes more difficult to maintain the solder mask webbing. At Bittele electronics, our solder mask webbing capabilities have a minimum of 3.5 mils for green solder mask oil for a board with 1oz copper weight. For any other colour, our minimum solder mask webbing is 4.5 mils. When moving to 2oz copper, our minimum solder mask webbing is increased by 1 mil to 4.5 mils for green solder mask oil. Similarly, for all other solder mask colours, the minimum solder mask webbing is also increased by 1 mil to 5.5 mils. This trend continues for 3oz copper weight.
What does this mean for your projects? If you have any components that have a fine pitch that is below our minimum specs listed above for a given copper weight and colour, we will not be able to fabricate the board with the solder mask webbing. This does not mean that the components can not still be placed, just that we will not be able to keep the webbing. In these cases, the risk of solder bridges are still minimal for STM assembly because it will still be controlled by the stencil. Bittele inspects all parts after assembly to ensure that no shorts have occurred.
Related Articles:
Please briefly describe the information you are seeking in the search bar below.