TURN-KEY PCB ASSEMBLY: BITTELE ELECTRONICS
PCB MANUFACTURING AND ASSEMBLY
Full Turn-Key PCB Manufacturer
You can quickly get quotes and order PCB fabrication and assembly using our online system. Take advantage of exclusive automatic discounts with our tool. Our BOM pricing tool ensures you receive the lowest price for your order.
START A TURN-KEY PCB ORDER
Functional Testing
Bittele Electronics offers Functional Testing (FCT) with its turn-key assembly services. Functional testing usually is performed after the circuit boards are assembled and AOI & visual inspections are finished. Testing as soon as possible permits us to discover and fix component breakdowns, manufacturing mistakes, or possible design errors early in the process, and to perform failure analysis quickly. As a result, customers can give an exceptional product to their clients in a short period of time. Functional testing is performed primarily to prevent manufacturing problems, including shorts, opens, missing components, or the placement of the wrong parts.
Functional testers typically use a computer that is connected to test points or a test-probe point in order to perform FCT. By running the software or firmware, we can figure out if the PCBs are acceptable or not depending upon their ability to meet specific requirements.
Functional testing is implemented through testing software, typically called firmware, and testing equipment such as digital multimeters, input/output PCBs, communication ports. Automated computer-based Functional Testing (FCT) is performed by assembly line workers who use testing software that connects to external equipment used for monitoring the DUT.
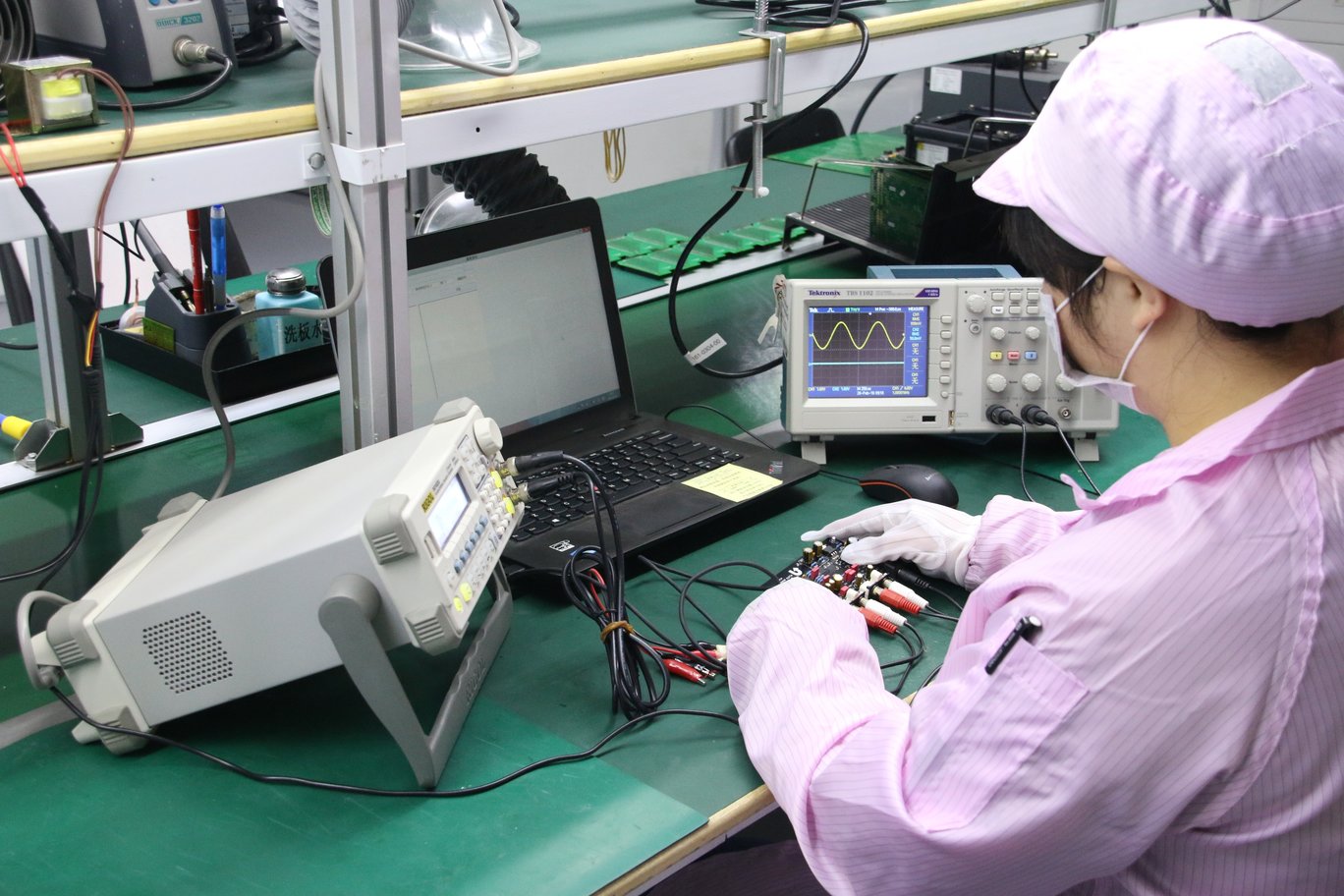
We would like to partner with you to help you execute your functional testing program. Our testing engineer will preview your requirements such as test scope and test instruction, design the test jig if necessary, set up the instruments, and prepare the test report form and design testing workflow.
At Bittele, we are equipped with an adjustable DC power supply, a 200MHz digital oscilloscope, a signal generator, an LCR multimeter and a universal programmer. This covers most embedded system testing. The test results can be either collected by a computer or recorded manually. If the board does not pass the testing, a troubleshooting program will be launched to find the root cause of the failure. A Design For Assembly (DFA) form will be issued by our process engineer and an 8D quality assurance report will be created by our quality engineer. The DFA report will be sent to the customer as a design reference. The latter will become our quality improvement guideline.